Aerospace steel tubes are an essential component of modern aircraft and spacecraft. They provide superior strength, durability, and corrosion resistance. These tubes are lightweight, allowing for greater fuel efficiency and better performance.
There are a variety of applications for aerospace steel tubes, ranging from structural frames to instrumentation systems. Selecting the right steel tubes for aerospace applications requires careful consideration of material grade and specifications.
In this article, we will explore the properties and advantages of aerospace steel tubes.
Key Takeaways
- Stainless steel is a preferred material in aviation and aerospace due to its superior strength and durability.
- Aluminum is widely used in the aerospace industry because of its lightweight nature and high strength-to-weight ratio.
- Both aluminum and stainless steel offer excellent corrosion resistance, making them suitable for aerospace applications.
- Stainless steel is known for its exceptional resistance to high temperatures, making it suitable for jet engine components and exhaust systems.
What are Aerospace steel tubes?
Aerospace steel tubes are metal cylinder-shaped tubes used in the aerospace industry for a variety of purposes. They are usually made from stainless steel or aluminum and offer a range of advantages such as corrosion resistance, weldability, and formability.
When selecting a material for aerospace steel tubes, it is important to consider specific properties such as temperature resistance, strength, and ductility. Manufacturing processes and techniques also play a key role in ensuring the tubes meet the desired specifications.
Additionally, the impact of temperature and pressure on tube performance must be taken into account. All these factors must be considered to ensure optimal performance and reliability.
With the right selection of materials, manufacturing processes, and considerations, aerospace steel tubes can provide superior performance, durability, and reliability for a wide variety of applications.
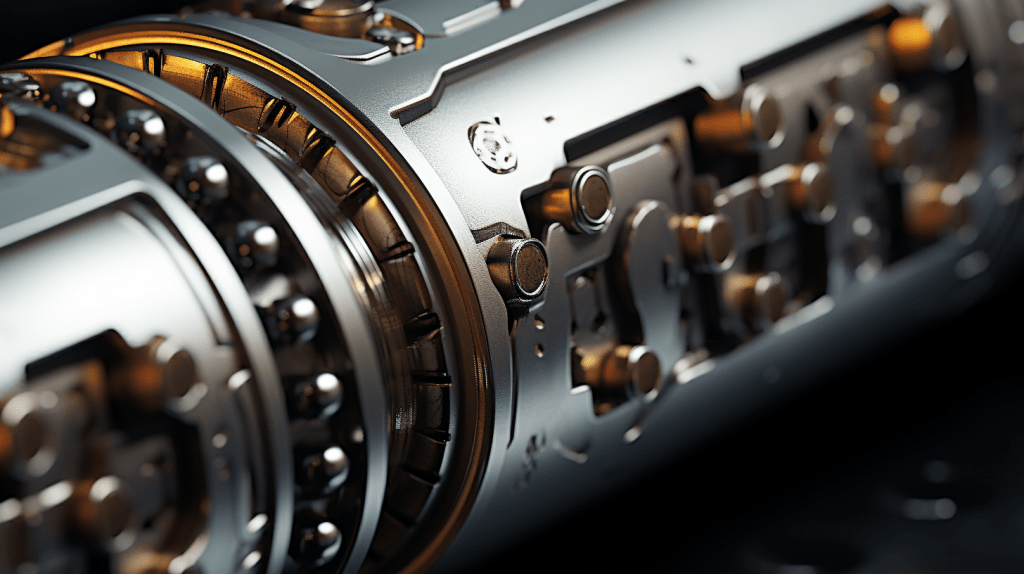
Applications
Aerospace steel tubes have a wide range of applications in defense, space, and commercial sectors. They are used in hydraulic and pneumatic control systems as well as cryogenic heat exchangers.
Additionally, they are often employed in structural applications such as aircraft frames, landing gear, and instrumentation systems.
DEFENSE
Six major defense applications of aerospace steel tubes include structural components, fuel systems, landing gear, fasteners, instrumentation, and control systems. Aerospace steel tubes possess certain properties that make them suitable for military applications, such as their high strength-to-weight ratio, corrosion resistance, cost-effectiveness, and adherence to strict manufacturing standards.
The use of aerospace steel tubes in defense applications is advantageous as they provide durability in harsh environments, are lightweight yet strong, and provide excellent corrosion resistance. They are also cost-effective and easy to maintain, making them an ideal choice for defense systems.
Benefits of Aerospace Steel Tubes in Defense Applications:
- High strength-to-weight ratio
- Excellent corrosion resistance
- Cost-effectiveness
- Strict manufacturing standards
SPACE
Steel tubes are used in various space applications, from providing structural components to support mission-critical systems. Aerospace steel properties, such as strength, durability, and corrosion resistance, make it an ideal choice for space exploration.
The steel tube manufacturing process is designed to produce tubes that are strong, lightweight, and highly resistant to corrosion. Stainless steel is the most commonly used type of steel in aerospace applications, due to its superior heat and corrosion resistance. Advantages of stainless steel include its strength, low weight, and durability, which make it suitable for use in space exploration.
Steel tube applications in space exploration include fuel tanks, landing gear, and engine components. Steel tubes are also used to construct frames and structures, as well as to house instrumentation and control systems. Steel tubes are highly corrosion resistant, which makes them ideal for use in a wide range of space applications.
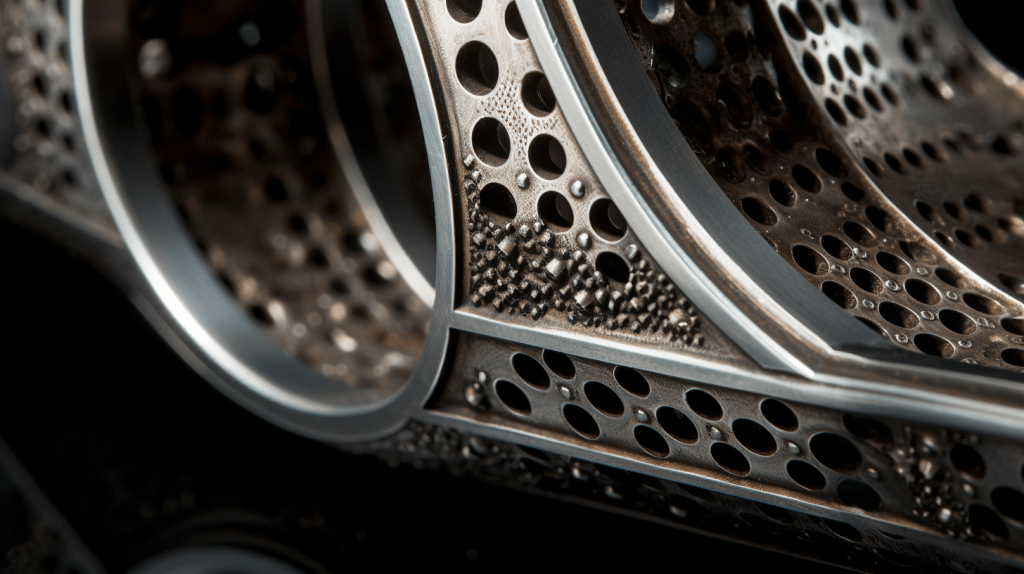
COMMERCIAL
In addition to its use in space exploration, aerospace steel tubes are also used in a variety of commercial applications. These include high-strength alloy tubing used in manufacturing processes and products, quality certifications to ensure tubing meets industry standards, titanium manufacturing standards for superior strength and lightweight, and high precision fabrications for exacting engineering applications.
Aerospace steel tubes are manufactured to exacting standards to ensure quality, reliability, and performance. They are used in a wide range of applications from commercial aviation to industrial manufacturing. Quality certifications ensure that the steel tubes meet industry standards for safety and reliability. The use of high-strength alloys and titanium manufacturing standards provide a superior strength-to-weight ratio, making them ideal for aerospace applications.
Hydraulic and pneumatic control systems
How is aerospace steel tubing used in hydraulic and pneumatic control systems? Aerospace steel tubing is used in a variety of control systems for a variety of applications. In hydraulic control systems, steel tubing is used to transport pressurized fluid from the power source to the actuator, which is then used to move the object as desired. In pneumatic control systems, steel tubing is used to transport pressurized air from the compressor to the actuator, which is then used to move the object as desired.
System | Applications |
---|---|
Hydraulic | Actuators, Valves, Motors, Cylinders |
Pneumatic | Actuators, Valves, Motors, Cylinders |
The use of steel tubing in aerospace hydraulic and pneumatic control systems allows for precise, reliable, and efficient operations. Steel tubing is durable and can withstand extreme conditions, making it an ideal material for use in these systems. Steel tubing is also easy to install and maintain, making it an ideal choice for many applications.
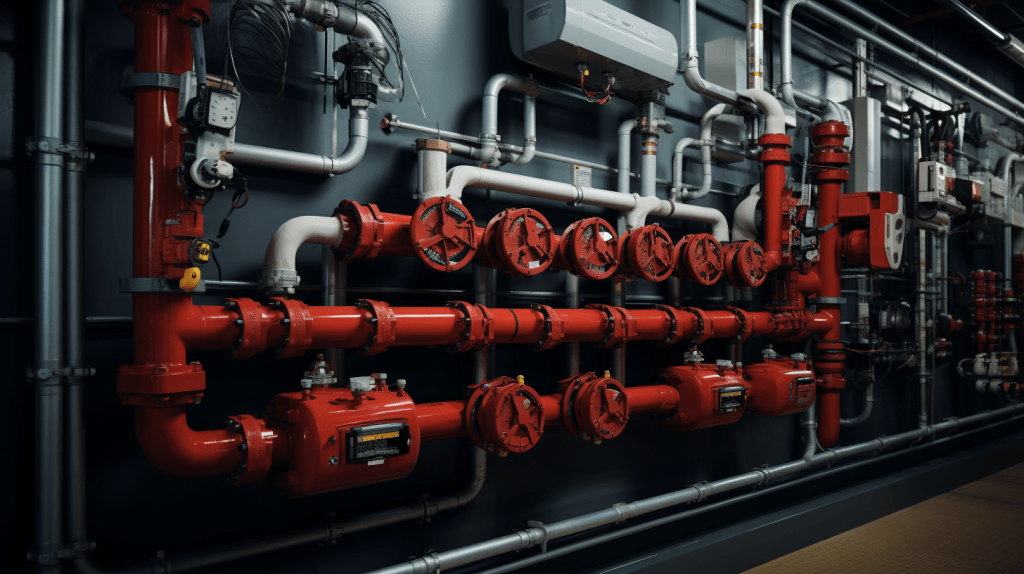
Cryogenic heat exchangers
Building upon the use of steel tubing in hydraulic and pneumatic control systems, cryogenic heat exchangers are also a common use of aerospace steel tubes. For cryogenic applications, material selection, welding techniques, and corrosion resistance are all considerations for ensuring optimal heat transfer efficiency.
Steel tubing is often chosen for its superior strength and durability, as well as its ability to withstand extreme temperatures and pressures. Additionally, welding processes are carefully chosen to ensure that the steel tubing is properly sealed and that the heat exchanger is leak-proof.
Finally, the corrosion resistance of steel tubing is essential for protecting the integrity of the heat exchanger. With these considerations, steel tubing is an excellent choice for cryogenic heat exchangers in the aerospace industry.
With this knowledge in mind, the next section will discuss the use of aerospace steel tubes in torque control rods.
Torque control rods
One of the primary applications of aerospace steel tubes is in torque control rods, which require excellent strength and durability. These components are integral for torque control mechanisms and must be able to withstand extreme conditions. In addition, they must be corrosion-resistant and able to function in all temperatures.
Material selection is an important factor when designing torque control rods, as is the manufacturing process used to create the tubes. Steel tubes are often preferred due to their superior strength and durability compared to other materials. However, due to their weight, engineers must make sure they are using the lightest steel tubes possible.
To this end, precision manufacturing processes are employed to ensure weight reduction without compromising strength. In this way, aerospace steel tubes can be used in torque control rods without sacrificing quality or performance.
Transmission tubes
When it comes to aerospace applications, steel tubes are often used for transmission purposes due to their strength and durability. Transmission tubes are manufactured to aerospace standards, ensuring precise dimensions and superior corrosion resistance.
Stainless steel tubing offers advantages such as excellent machinability, low weight, and good heat transfer properties. Aerospace steel tubes must also meet stringent weight requirements while still providing sufficient strength and corrosion resistance.
Manufacturers must ensure that the tubes adhere to the strictest manufacturing standards and meet the highest corrosion resistance requirements. Weight considerations must also be taken into account when selecting steel tubing for aerospace applications.
Convoluting/seals
Additionally, steel tubing can also be used for convoluting or sealing in aerospace applications. Convolute tubes provide superior seal performance and are highly resistant to environmental conditions, making them ideal for aerospace sealing applications.
Convoluting offers various advantages such as increased sealing surface area, improved fatigue life, and enhanced sealing capability. Convoluted tubes can be used for a range of sealing mechanisms including pressure seals, radial seals, and self-energizing seals.
Additionally, they can be used for a variety of sealing solutions in aerospace applications such as fuel and oil lines, hydraulic systems, and other components. Convoluted tubes are an ideal choice for applications that require reliable and robust sealing solutions.
Ducting systems
Ducting systems are a common application for aerospace steel tubes. They are used in aircraft construction for their material properties, including corrosion resistance and high mechanical strength. Weight reduction is also a major factor in choosing steel tubes for ducting systems. Steel tubes are lightweight and durable, making them an ideal choice for aircraft application.
Additionally, steel tubes offer superior corrosion resistance which makes them highly suitable for use in damp environments. Steel tubes are also low maintenance and can withstand high temperatures, making them an ideal choice for use in aircraft construction. These factors make steel tubes a popular choice for ducting systems in the aerospace industry.
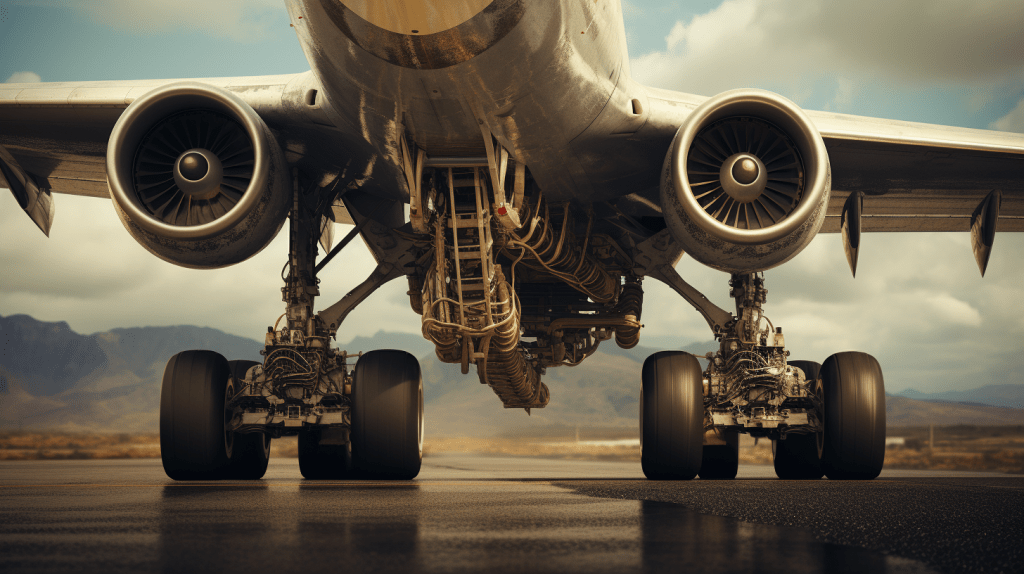
Landing gear
For aerospace applications, steel tubes are often used in the construction of landing gear due to their strong, lightweight, and corrosion-resistant properties. They are used in hydraulic control systems, torque control rods, waveguides, and fuel pipes. Steel tubes have the added benefit of being able to withstand high pressures and temperatures which makes them ideal for landing gear.
Steel tubes have a high strength-to-weight ratio and are highly resistant to fatigue damage, making them a perfect fit for aircraft landing gear. Steel tubes are also easy to fabricate and maintain which makes them more cost-effective in the long run.
Waveguides are also an important component in aircraft landing gear due to their ability to transmit signals across long distances. This makes them an essential part of the aircraft control system.
Steel tubes are an integral part of the aerospace industry due to their versatility and reliability in landing gear applications. With their strength, durability, and corrosion resistance, steel tubes are the ideal material for aircraft landing gear.
Moving on, we will now discuss waveguides and their importance in the aerospace industry.
Waveguides
The application of waveguides in aerospace is significant, as they are used to transmit signals across long distances in aircraft control systems. They are typically constructed from metal, ceramic, or composite materials, and require precise fabrication techniques to ensure optimal performance.
Design considerations must also be taken into account, such as the size, shape, and electrical characteristics of the waveguide. These applications include wireless communication, navigation systems, radar systems, and more. The waveguide’s performance is heavily dependent on the materials and fabrication process used, and any design modifications must be weighed carefully.
From fuel pipes to waveguides, aerospace steel tubes are essential components in the aerospace industry.
Fuel pipes
Building upon the importance of waveguides in aerospace, fuel pipes are equally essential components for aircraft. Fuel pipe materials must provide strong corrosion resistance and structural integrity while being lightweight. They often utilize stainless steel, aluminum, or titanium alloys.
Fuel pipe manufacturing processes must meet strict industry standards and include welding, brazing, and/or soldering. Pressure ratings must be checked to ensure the pipe can withstand the expected pressure and flow of fuel. The fuel pipe installation must adhere to the manufacturer’s guidelines for proper fit and function.
Corrosion resistance must be achieved through the use of protective coatings and treatments. Fuel pipes must also be regularly inspected for wear and tear and any signs of corrosion. These measures ensure that fuel pipes are reliable and safe for use in aerospace applications.
The next section will discuss the importance of instrumentation in aerospace.
Instrumentation
An important application of instrumentation in aerospace is the use of steel tubes. Instrumentation advancements have revolutionized the aviation industry, enabling more efficient aircraft designs and improved safety.
The future trends in aerospace instrumentation include smart sensors, wireless networks, and autopilots. Instrumentation challenges in the aerospace industry include the integration of multiple systems, developing new technologies for extreme environments, and ensuring the reliability of data.
Instrumentation has a significant impact on aviation safety, as it helps detect and prevent potential problems in the aircraft. Additionally, it plays a key role in aircraft maintenance, allowing engineers to monitor the performance of the aircraft and make necessary repairs.
Types of stainless steel tubes used in aerospace
Stainless steel has become an increasingly popular material for aerospace applications due to its superior strength, durability, and corrosion resistance.
In this article, we will discuss the various types of stainless steel tubes used in aerospace. These include hydraulic tubing lines, which are used to transmit fluid power in aircraft systems.
Instrumentation tubes are another type of stainless steel tube commonly used in aerospace. These tubes are used to carry various instruments and sensors that measure and monitor different parameters in the aircraft.
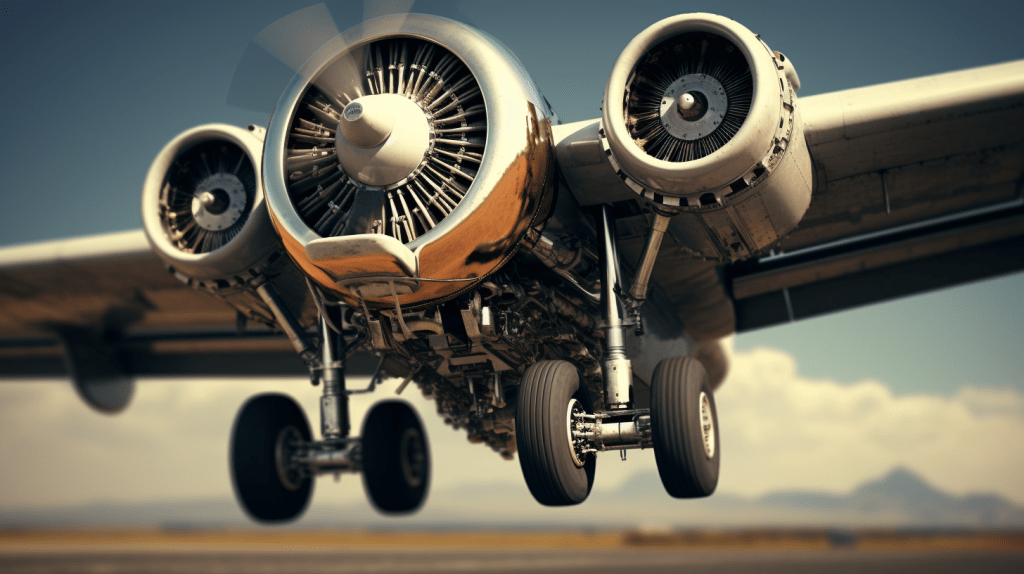
Pitot tubes, which are used to measure the airspeed of an aircraft, are also made from stainless steel.
Convoluting/seal tubes, on the other hand, are used to provide flexibility and sealing capability in aerospace applications.
Finally, engine fuel lines are another important application of stainless steel tubes in aerospace. These tubes are responsible for carrying fuel from the fuel tanks to the aircraft engines.
Hydraulic tubing lines
The aerospace industry’s use of stainless steel tubes includes a variety of hydraulic tubing lines. These lines are integral components of the aircraft’s hydraulic systems and must be made to the highest standards of precision and quality. When selecting hydraulic tubing materials, corrosion resistance, strength, and heat resistance must be considered. Tubing fabrication techniques must also be adapted to aerospace industry regulations and the specific requirements of the system.
These techniques range from cold-forming and welding to cutting and machining. To make sure that the tubing lines meet the highest standards, it is important to ensure that the material selection, fabrication, and installation are all done correctly. In addition, regular inspections should be done to check for any potential signs of wear and tear.
Instrumentation
Many aircraft instrumentation systems rely on stainless steel tubes to accurately detect, measure, and control various parameters. These instrumentation tubes must meet stringent quality standards and must be resistant to corrosion, oxidation, and other environmental factors. In addition, they must be able to withstand high torque control and waveguide applications.
The quality of the tubing used in instrumentation systems is certified by organizations such as ASME and ASTM. Depending on the application, the tubing can be made of various grades of stainless steel and nickel alloys. Aluminum is also used in some defense sector applications.
To ensure that instrumentation tubing is of the highest quality, manufacturers must adhere to strict production standards and procedures. They must also pay close attention to the manufacturing process, including the selection of raw materials, quality control, and testing. This ensures that the tubing is safe and reliable for use in aerospace instrumentation systems.
Pitot tubes
Pitot tubes are commonly used in aerospace applications. They typically consist of stainless steel tubing and are designed to measure static and dynamic pressure to measure the speed of a moving object. Pitot tubes are used in aircraft to measure airspeed. They are also used to measure the speed of liquids in pipes and tanks. Proper pitot tube design, calibration, maintenance, and performance are essential for accurate measurements.
In aerospace, pitot tube applications include aircraft flight instruments, wind tunnels, air data computers, and other systems. Pitot tubes are also used in industrial systems such as hydraulic pressure and flow rate sensors. It is important to carefully inspect and test the pitot tube to ensure accuracy and reliability. Regular maintenance and calibration are also necessary to ensure optimal performance.
Convoluting/seals
Building on the previous discussion of Pitot tubes, convoluting and seals are two types of stainless steel tubes commonly used in aerospace applications. Convoluting technology allows for complex bends and shapes to be formed in steel tubes, providing strength and a high level of precision.
Sealing solutions involve welding techniques to create a secure connection between two tubes and ensure resistance to corrosion and leakage. Aerospace tube bending is a specialized process that requires experienced professionals to ensure accurate and reliable results.
With welded solutions, advanced welding techniques are used to provide the highest quality and most reliable sealing solutions. Stainless steel is the preferred material for aerospace applications due to its excellent corrosion resistance and strength.
All of these processes must be done carefully and precisely to ensure the highest quality and safety of the finished product. With the right materials and expertise, aerospace tube bending and welding can provide reliable and secure sealing solutions.
This transitions into the next section about engine fuel lines.
Engine fuel lines
Transitioning from convoluting and seals, engine fuel lines are a critical component of aerospace systems. They require the use of stainless steel tubes, which offer superior strength and durability. Aluminum alloys are chosen for their excellent corrosion resistance and ability to allow for weight optimization. Material selection and welding techniques are essential for ensuring long-term performance. Advanced techniques are used for precise fabrication and assembly.
- Aluminum alloys provide corrosion resistance and weight optimization.
- Material selection and welding techniques are essential for longevity.
- Stainless steel tubes offer superior strength and durability.
- Advanced techniques are used for precise fabrication and assembly.
Heat exchanger tubes
In aerospace applications, heat exchanger tubes are typically constructed from stainless steel for superior strength and durability. The material is well-suited for this purpose due to its excellent corrosion resistance and high material strength. Additionally, due to its weldability, stainless steel offers cost-effectiveness when compared to other heat exchanger materials.
However, weldability considerations should also be taken into account when choosing a material for this application. The cost-effectiveness, corrosion resistance, and material strength of stainless steel make it an ideal choice for heat exchanger tubes in aerospace applications. As such, it is a popular choice for this purpose.
With that in mind, the next section will explore the advantages and disadvantages of the CDV6 tube.
15CDV6 TUBE
A popular type of stainless steel tube used in aerospace applications is the Chromium-molybdenum-vanadium alloy known as 15CDV6. This alloy is known for its outstanding yield strength after heat treatment, making it suitable for pressure vessels, wishbones, and suspension components. 15CDV6 is easily welded without requiring localized heat treatment after welding and is commonly used in motorsport applications, as well as rocket motor casings and track and push rods.
When designing aerospace structures, it is important to consider the advantages and disadvantages of aluminum and stainless steel. Aluminum is lightweight and has a high strength-to-weight ratio, but is not as heat resistant as stainless steel. Stainless steel is highly durable and corrosion-resistant but is heavier than aluminum.
15CDV6 offers a good compromise between the two materials, providing the strength and durability of stainless steel with the lightweight properties of aluminum.
1020 TUBE
Switching gears, 1020 TUBE is a type of stainless steel tube that is commonly used in aerospace applications. It is a popular choice due to its superior corrosion resistance in aerospace environments. The tube manufacturing process involves forming, bending, and welding to create the desired shape for the aerospace tubing materials.
1020 TUBE is also ideal for aerospace tube bending and welding, making it an excellent choice for high-performance applications. Its lightweight, yet durable properties make it the perfect option for aerospace applications that require extreme temperature resistance and strength. The tube’s superior corrosion resistance also makes it a great choice for applications that are exposed to harsh environments.
1020 TUBE is an ideal choice for aerospace applications that require superior performance and durability.
As we move on to discuss the subtopic of ‘t45 tube’, it is important to note that its properties make it suitable for applications where high precision and strength are required.
T45 TUBE
Building on the discussion from the previous subtopic, the T45 Tube is a type of stainless steel tube that is commonly used in aerospace applications due to its superior corrosion resistance and strength. It has several advantages, including high strength, easy to form and weld, and improved structural strength without adding too much weight.
Typical applications include roll cages, space frames, aerospace impact protection, roll bars, pilot seats, and crew seats. Additionally, it can be welded using various techniques and its manufacturing process is also well-defined.
T45 Tube is superior to other steel alloys in terms of corrosion resistance and strength, making it an ideal choice for aerospace applications. With the help of technical assistance and additional information, the T45 Tube can be used with confidence in any aerospace application.
This transitions to the discussion of stainless steel and its various uses in the aerospace sector.
304 STAINLESS STEEL
Stainless steel is a preferred material for aerospace applications due to its superior strength, corrosion resistance, and durability. Its advantages include its relatively low weight and high strength-to-weight ratio, as well as its excellent corrosion resistance. In addition, stainless steel components are easier to clean and maintain, making them ideal for aerospace applications. When manufacturing aerospace components out of stainless steel, it is important to adhere to strict standards to ensure the highest quality and safety.
When it comes to aerospace applications, aluminum and stainless steel are often compared. Aluminum is lighter than stainless steel, but stainless steel has a higher melting point and tensile strength. However, aluminum has a lower weight density than stainless steel. Depending on the application, one material may be more suitable than the other. Ultimately, the choice between aluminum and stainless steel should be based on the weight requirements, environmental conditions, temperature and heat resistance, and maintenance and cleaning considerations.
21-6-9 STAINLESS STEEL
In addition to aluminum, 6-9 stainless steel is another commonly used material for aerospace applications. It is a high manganese nitrogen-strengthened austenitic stainless steel with excellent resistance to oxidation and lead oxide at high temperatures. This type of stainless steel offers high strength in the annealed condition and is suitable for applications such as aircraft components, steam and autoclave parts, and chemical equipment.
The stock size range for 21-6-9 stainless tubing is 0.188 – 3.00 with a wall range of 0.016 – 0.083. Some of the key properties of this stainless steel include a minimum weight of 5.50 manganese, 19.00 chromium, 8.00 nickel, 0.15 nitrogen, ultimate strength of 120 KSI (827 MPA), and yield strength of 142-162 KSI (979-1117 MPa). It is recommended to follow rigorous manufacturing standards to ensure corrosion resistance and durability.
Aluminum and stainless steel have their benefits and drawbacks, and the choice of material depends on the application’s weight requirements, environmental conditions, and other factors.
This concludes the discussion about 6-9 stainless steel in aerospace applications. Now let’s move on to discuss the properties, applications, and pipe size options of stainless aerospace tubing.
347 STAINLESS AEROSPACE TUBING
Stainless steel is a popular choice for manufacturing aerospace tubing due to its exceptional strength and resistance to high temperatures.
347 stainless steel is an austenitic alloy, alloyed with columbian-tantalum for good mechanical properties. It is widely used in aerospace applications and has excellent intergranular corrosion resistance. It can withstand temperatures up to 1500°F.
Pipe sizes range from .031-3.00′ OD and wall range from .020-.156′. Chemical composition and mechanical properties vary depending on the pipe size and wall thickness.
DFARS compliance for 347 stainless aerospace tubing is yes for some sizes and no for others.
Manufacturing standards for aerospace tubing include MIL-T-8808, MIL-T-8606, AMS 5556, and AMS 5571.
321 STAINLESS STEEL
Manufacturing with stainless steel provides excellent strength and durability for aerospace applications. It is highly resistant to corrosion and has many beneficial properties for aerospace tubing materials. Stainless steel is a popular choice due to its high tensile strength, low thermal expansion, excellent ductility, and high resistance to wear and tear.
Stainless steel is manufactured to stringent standards to ensure high quality for aerospace steel applications. It is a cost-effective option that meets the requirements for corrosion-resistant and high-temperature materials. It can be formed and machined to tight tolerances and comes in a variety of forms and sizes.
Stainless steel is the perfect choice for aerospace projects due to its superior strength and durability.
T64 TUBE
T64 steel tube is a carbon manganese steel material, providing high tensile strength and a hardness lower than T45, making it an ideal choice for weight-critical aerospace applications. The manufacturing process involves cold-rolling and heat treatment, resulting in a lightweight alloy that offers a good strength-to-weight ratio.
T64 steel tube is used for superheater tubes, cooling tubes, furnace tubing, oil & gas sector applications, and aerospace applications. It has advantages such as high strength with good hardness, and lightweight alloy. However, it has some limitations such as its lack of corrosion resistance.
Future developments are focusing on improving corrosion resistance and creating new alloys to replace T64 tubes. Alternative materials include aluminum and stainless steel, which offer better corrosion resistance.
High Strength and Lightweight Alloys
In the aerospace industry, high-strength and lightweight alloys play an important role in the construction of steel tubes. These alloys include titanium, stainless steel, and nickel alloys which offer superior strength and corrosion resistance.
Titanium
Titanium alloys provide an excellent balance of strength, lightweight, and corrosion resistance, making them ideal for use in aerospace steel tubes. Titanium is used in many applications such as airframes, engines, and landing gear. It is also highly resistant to fatigue, allowing for the construction of lighter, stronger, and more durable components. Manufacturing standards for titanium alloys are extremely stringent to ensure that they meet the demands of the aerospace industry.
When compared to aluminum, titanium is much stronger and lighter. It also offers superior corrosion resistance, making it a more reliable and durable choice for aerospace applications. Titanium alloys are also more resistant to extreme temperatures than aluminum, making them suitable for aerospace steel tubes in extreme conditions.
- Titanium alloys provide high strength and lightweight
- Superior corrosion resistance compared to aluminum
- Manufacturing standards for titanium are stringent
- Titanium is more resistant to extreme temperatures
Stainless steels
Stainless steels are high-strength and lightweight alloys that are widely utilized in the aerospace industry. They can be manufactured in several forms such as sheets, tubes, and rods, and are known for their excellent corrosion resistance, making them ideal for aerospace applications. These alloys offer a weight-to-strength ratio that is superior to most other materials, making them an invaluable option for aircraft and space vehicles. The aerospace steel properties also include excellent thermal conductivity and formability, allowing for easy fabrication and assembly.
Manufacturing of aerospace steel tubes requires high precision and advanced techniques to ensure that the parts meet the necessary safety standards. These alloy tubes are used in a variety of applications, from airframes and engines to landing gear and instrument systems. The high strength and light weight of stainless steel make them the perfect choice for aircraft and spacecraft components.
The transition from stainless steels to nickel alloys will introduce an even higher level of strength and durability, making them suitable for a range of demanding applications.
Nickel alloys
Nickel alloys provide an even higher level of strength and durability for aerospace steel tubes by offering a range of benefits to aerospace steel manufacturing. These alloys increase corrosion resistance, improve weight considerations, and enhance strength. They are also well-suited for high-stress applications, making them suitable for a wide variety of aerospace tubing certifications.
Nickel alloys are highly versatile and can be used in a variety of aerospace applications. They are commonly used in airframes and structural components, as well as aircraft engines and landing gear. With their superior strength and corrosion resistance, nickel alloys are an ideal choice for aerospace manufacturers who require strong, lightweight components.
Typical Aerospace Grades and Specifications
Typically, aerospace-grade steel tubes offer superior strength and durability, making them a suitable choice for many applications. These tubes are typically made from a variety of alloying elements such as carbon, chromium, molybdenum, and nickel, to name a few. The combination of these materials allows aerospace-grade steel tubes to be highly resistant to corrosion, temperatures, and stress. Additionally, they are capable of holding up to extreme changes in temperature and pressure.
Aerospace-grade steel tubes are used in a variety of applications such as aircraft engine components, hydraulic cylinders, and pressure vessels.
Product Specs:
- Variety of alloying elements
- Highly resistant to corrosion, temperatures, and stress
- Capable of withstanding extreme changes in temperature and pressure
Pros:
- Superior strength and durability
- High resistance to corrosion and temperature
- Easy to form and fabricate
- Low maintenance requirements
Cons:
- Higher cost than other metals
- Require specialized tools for fabrication
- May require special handling due to weight
Titanium Manufacturing Standards
When it comes to titanium manufacturing standards, they are often among the highest in the industry due to the material’s superior strength and durability. The manufacturing processes used to create aerospace steel tubes must be carefully controlled to achieve the necessary corrosion resistance and strength. The fabrication of these tubes is a complex process involving precision measurements, specialized tools, and stringent quality control. Aerospace steel tube suppliers must adhere to the highest standards of quality to guarantee their products are safe and reliable.
The testing and evaluation of titanium tubes is an important factor in the aerospace steel industry. From destructive testing to non-destructive inspection, all aerospace steel tubes must meet the required standards before they can be used in aircraft and space vehicles. Additionally, suppliers must be able to provide detailed documentation of the materials used and the processes employed throughout the manufacturing process.
The following are some of the key aspects of titanium manufacturing standards:
- Titanium manufacturing processes must adhere to strict quality control and safety regulations.
- Aerospace steel tubes must provide excellent corrosion resistance and strength.
- Aerospace steel tube fabrication requires precise measurements and specialized tools.
- Aerospace steel tube suppliers must be able to provide detailed documentation and testing results.
Stainless Steel Manufacturing Standards
Highly stringent quality control standards are employed in the manufacturing of aerospace stainless steel tubes. To ensure the highest quality and performance, manufacturers must adhere to strict guidelines and specifications.
The properties of stainless steel, such as corrosion resistance, strength, and durability, are essential for use in aerospace applications. Manufacturing processes must also be carefully monitored to ensure the steel is of the highest grade.
To achieve the desired level of corrosion resistance, stainless steel must be treated with special coatings and finishes. The steel must also be heat-treated to increase its strength and durability. To ensure the highest quality standards, manufacturers must use specialized equipment and tools to shape and form the steel.
To ensure the steel tubes are of the highest quality, rigorous testing must be performed during the manufacturing process. These tests include tensile strength tests, hardness tests, and corrosion tests. The results of these tests must be carefully reviewed before the steel is approved for use in aerospace applications.
The use of stainless steel in aerospace applications is highly regulated and must meet the highest standards for quality and performance. By adhering to the strict manufacturing standards, aerospace steel tubes will be able to meet the demands of the most challenging applications.
Nickel Alloy Manufacturing Standards
Manufacturers must adhere to strict guidelines and specifications when manufacturing nickel alloys for aerospace applications. Nickel alloys have superior corrosion resistance and are highly resistant to high temperatures, making them ideal for aerospace applications. The fabrication of aerospace steel tubes requires a high level of precision and the use of advanced manufacturing techniques. To ensure the tubes are of a high quality, manufacturers must adhere to strict quality control standards. Additionally, the impact of temperature on the steel tubes must be considered, as it can affect their structural integrity.
To meet the demands of aerospace applications, there has been an increase in the development of nickel alloy manufacturing techniques. Advanced technologies such as laser welding and forming have been developed to improve the accuracy and speed of the manufacturing process. Furthermore, advancements in corrosion resistance in aerospace materials have enabled manufacturers to create steel tubes that are more durable and reliable.
TUBING QUALITY
Steel tubes used in aerospace applications must meet strict quality standards to ensure optimal performance and safety. To ensure that these standards are met, steel tubing manufacturers must adhere to rigorous quality certifications and manufacturing standards.
This article will explore the various tubing quality certifications and manufacturing standards used in the aerospace industry.
TUBING QUALITY CERTIFICATIONS
Frequently, aerospace steel tubes must meet certain quality certifications to ensure safety and reliability. Such certifications include corrosion resistance comparison, benefits of stainless steel, aerospace steel grades, and manufacturing standards.
These certifications are essential for the production of aerospace steel tubes, as they demonstrate the product’s quality and ability to meet the manufacturing standards. Stainless steel offers superior strength and durability, excellent corrosion resistance, and low maintenance requirements. This makes it an ideal material for aerospace applications.
Furthermore, aerospace steel grades provide greater strength and durability, while ensuring that the steel meets the necessary manufacturing standards. By meeting these tubing quality certifications, aerospace steel tubes can provide greater safety and reliability in the aviation and aerospace industries.
This transitions into the next section about the importance of manufacturing standards.
MANUFACTURING STANDARDS
To ensure the highest quality of aerospace steel tubes, manufacturers must adhere to strict manufacturing standards.
The standards for these tubes include tubing quality certifications such as ASTM, ASME, and API standards. These certifications guarantee that the tubes meet the requirements for use in aerospace applications.
Other important factors to consider are the differences between aluminum and stainless steel products. Stainless steel has superior strength and durability, while aluminum offers a lighter-weight option.
Both materials offer a variety of benefits for aerospace applications, and manufacturers must consider the specific requirements for each project to choose the best material for the job.
Ultimately, manufacturers must adhere to strict manufacturing standards and certifications to ensure the highest quality of aerospace steel tubes. This is vital to guarantee the safety and performance of aerospace components and systems.
Aluminum vs. Stainless Steel in aerospace
When it comes to aerospace applications, both aluminum and stainless steel have their unique advantages and drawbacks.
In this article, we will discuss the differences between aluminum and stainless steel, the benefits of each, their applications in aviation and aerospace, and the factors to consider when choosing between them.
Why Is Aluminum Used in Aircrafts and Aviation?
The aerospace industry often relies on the strength-to-weight ratio and corrosion resistance of aluminum to select it as a material for aircraft and aviation over stainless steel.
The advantages of aluminum include its lightweight properties, high strength-to-weight ratio, excellent corrosion resistance, good thermal conductivity, and ease of forming and fabricating.
Stainless steel is superior in terms of its strength and durability, excellent heat resistance, and corrosion resistance.
Aluminum is used for aircraft frames and structures, interior components, engine components, and fuel tanks and storage systems.
Stainless steel is used for jet engine components, exhaust systems, landing gear, fasteners and connectors, and instrumentation and control systems.
Key factors to consider when choosing between aluminum and stainless steel are weight requirements, environmental conditions, temperature and heat resistance, maintenance and cleaning, and cost-effectiveness.
Why Is Steel Used in aircraft and Aviation?
While aluminum is preferred in many aerospace applications, steel offers several benefits that make it a suitable material for aircraft and aviation, especially when compared to aluminum and stainless steel.
Steel has superior strength and durability, making it an excellent choice for jet engine components and exhaust systems. Its exceptional heat resistance makes it ideal for landing gear and fasteners. Additionally, its high corrosion resistance makes it a great material for instrumentation and control systems.
When selecting a material for aerospace applications, it is important to consider the advantages of both aluminum and steel. Steel is a more robust option than aluminum, while stainless steel offers a higher tensile strength than aluminum. Furthermore, when it comes to weight, aluminum has a lower weight density than stainless steel.
Ultimately, the selection of a material should be based on the application’s weight requirements, environmental conditions, temperature, and budget constraints.
To transition into the next section, we will explore the advantages of aluminum in aviation and aerospace.
Aluminum in Aerospace
An article on ‘Aerospace Steel Tubes’ would be incomplete without a discussion of aluminum’s role in the aerospace industry. Aluminum is a lightweight material that is widely used in the aviation and aerospace industry due to its advantages such as high strength-to-weight ratio and excellent corrosion resistance. In comparison to stainless steel, aluminum has a lower weight density and a lower tensile strength. However, stainless steel offers superior strength and durability as well as exceptional resistance to high temperatures which are essential properties for aerospace applications.
Aluminum is widely used in aircraft frames and structures, interior components such as seats and panels, engine components, fuel tanks and storage systems, and heat exchangers and radiators due to its advantages. Stainless steel, meanwhile, is used for jet engine components, exhaust systems, landing gear, fasteners and connectors, and instrumentation and control systems.
When choosing between aluminum and stainless steel, factors such as weight requirements, environmental conditions, temperature and heat resistance, maintenance and cleaning considerations, and cost-effectiveness must be considered. Ultimately, both materials offer benefits that make them suitable for aerospace applications, and understanding their differences is key to finding the right material for the job.
Stainless Steel in Aerospace
Stainless steel provides many advantages for aviation and aerospace applications, making it an ideal choice for components such as jet engine components, exhaust systems, landing gear, fasteners, and instrumentation systems.
Its superior strength and durability, excellent resistance to high temperatures, and corrosion resistance make it a highly sought-after material for these industries.
Stainless Steel Products for Aviation and Aerospace Manufacturing
Due to its superior strength, durability, corrosion resistance, and heat resistance, stainless steel is an ideal material for various aviation and aerospace manufacturing applications. It is widely used for components such as jet engine parts, exhaust systems, landing gear, instrumentation, and control systems. Stainless steel is also used for fasteners, connectors, and other structural components. Its hygienic properties and easy-to-clean surface make it an attractive material for interior components such as seats and panels.
When selecting stainless steel products for aviation and aerospace manufacturing, the following factors should be considered. Weight requirements, environmental conditions, temperature and heat resistance, maintenance and cleaning needs, and cost-effectiveness are all important considerations. Quality assurance is also essential to ensure that parts meet aviation and aerospace standards.
Product Specs:
- High strength and durability
- Superior corrosion and heat resistance
- Hygienic and easy to clean
- Low maintenance
- Variety of grades and sizes
Pros:
- Lightweight yet strong material
- Exceptional resistance to high temperatures
- Excellent corrosion resistance
- Low maintenance requirements
- Easy to form and fabricate
Cons:
- Costlier than other materials
- Complex to manufacture
- Difficult to weld
- Susceptible to stress corrosion cracking
Frequently Asked Questions
What Are the Advantages of Using Aerospace Steel Tubes?
Aerospace steel tubes offer a range of advantages, such as improved heat treating and welding techniques, superior corrosion and fatigue resistance, and metallurgical properties. For example, Airbus used aerospace steel tubes to construct the A320’s fuselage, resulting in an aircraft that is both strong and lightweight.
Are Aerospace Steel Tubes More Expensive Than Other Metals?
Cost comparison between aerospace steel tubes and other metals depends on quality standards, corrosion protection, and performance. A cost-benefit analysis should be conducted to determine the optimum option for a given application.
What Are the Benefits of Using Titanium in Aerospace Applications?
Titanium is like a superhero in aerospace applications, offering strength, heat resistance, weight reduction, and unparalleled durability. Compared to other metals, titanium is often more cost-efficient, making it the ideal choice for missions that require high performance and reliability.
How Do Aerospace Steel Tubes Compare to Aluminum and Stainless Steel?
Steel tubes used in aerospace applications offer superior strength and weight ratio, corrosion resistance, and better heat treating and welding capabilities compared to aluminum and stainless steel. Their alloy composition also provides better strength and durability.
What Safety Standards Are Used to Ensure the Quality of Aerospace Steel Tubes?
Strict safety standards ensure the quality of aerospace steel tubes. A rigorous certification process, comprehensive quality control, cost comparisons, and strength testing are all part of the manufacturing process. Meticulous attention to detail is paramount to ensure the superior strength and reliability of these critical components.
Conclusion
In conclusion, aerospace steel tubes offer many advantages in aerospace applications. This is due to their strength, durability, and resistance to high temperatures. Additionally, they are lightweight, which increases fuel efficiency and leads to better overall performance.
Steel tubes are also a more cost-effective choice than other materials such as aluminum. On average, aerospace steel tubes are about 40-50 percent lighter than aluminum. They also have a tensile strength that is up to three times greater.
Overall, aerospace steel tubes provide a combination of strength, durability, resistance to high temperatures, and lightweight properties. This makes them an ideal choice for various aerospace applications.