Alloy steel tubing is an advantageous choice for a variety of applications due to its superior strength and toughness, high strength-to-weight ratio, and superior machinability. It is available in a wide variety of grades and sizes to meet the needs of multiple industries. These industries include commercial aircraft, automotive, machine tools, hydraulic tools, aerospace, and oil and gas.
Metal Special is a leading distributor of alloy steel tubing. They offer quality products backed by on-time delivery.
Key Takeaways
- Alloy tubing is manufactured using different processes such as CDS, HRS, and DOM, following ASTM A513 Type 5 or ASTM A519 industry standards.
- Alloy round mechanical tubing offers superior tensile strength, toughness, and a high strength-to-weight ratio. It can be easily heat treatable and is suitable for various processing techniques.
- 4130 and 4140 alloy tubing are the easiest to machine among common alloy grades and are suitable for machined parts, wear parts, fixtures, mold bases, gears, and more.
- Alloy tubing is available in a wide range of sizes, allowing for flexibility in dimensions. It is used in various applications such as automotive, transportation, aircraft frames, bicycle frames, shafts, roll cages, and control arms.
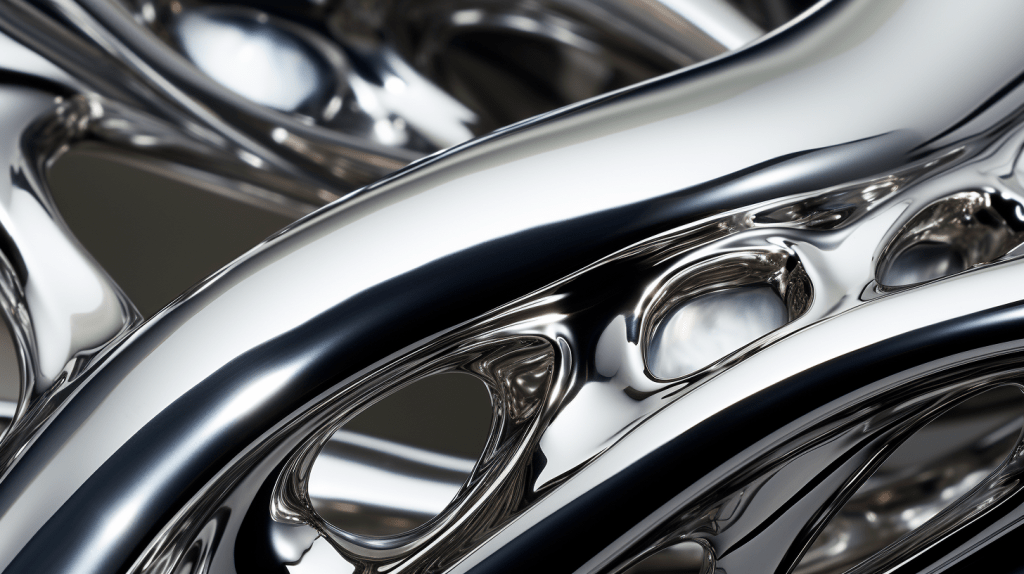
ALLOY ROUND MECHANICAL TUBING
Alloy round mechanical tubing offers superior strength and toughness due to its high strength-to-weight ratio. Manufacturing processes such as CDS, HRS, and DOM are used to produce the tubing according to ASTM A513 Type 5 or ASTM A519 industry standards.
Alloy round mechanical tubing is an excellent candidate for machining techniques where strength is required, such as for parts, fixtures, mold bases, gears, and more. It also offers the ability to customize and control the size of the tubing, which makes it a great option for a variety of applications.
Supply chain management is also made easier with Metal Special inventory, resources, and capabilities to meet material needs.
Alloy round mechanical tubing provides reliable and durable solutions that can be used in a variety of industries.
4140/4142 Alloy Steel Tubing
Building on the discussion about alloy round mechanical tubing, 0/4142 is a chromium-molybdenum alloy that is widely used and versatile in machinery steel applications. Characterized by superior tensile strength and toughness, this alloy is heat treatable to a broad range of strengths, machinabilities, and hardnesses. It is an excellent candidate for processing techniques where strength is required and is also easy to machine. 0/4142 has added elements such as manganese and nickel to improve its strength, hardness, and toughness.
The alloy steel properties of 0/4142 make it suitable for applications in the automotive and transportation industry, aircraft frames, bicycle frames, shafts, collars, roll cages, control arms, and A-arms. It is also resistant to sour gas environments and conforms to NACE Standard MR01-75. With its high-quality alloy tubing, Metal Special offers 0/4142 in a wide range of sizes, from rolled bar to pierced or cold drawn.
Heat treatment of 0/4142 is necessary to meet ASTMA434CLBC/BD requirements. Forging should commence at 1200 max and finish at 950. Annealing should be done at 815/850 and cooled slowly in a furnace. Normalizing should be done at 870/900 and cooled in air. Hardening and tempering should be done at 820/870 and oil quenched, with tempering usually above 430 and up to 700.
4130 (E4130) Alloy Tubing
Continuing on from 4140/4142, 0 (E4130) alloy steel is a chromium-molybdenum alloy that is widely used and versatile in many applications. It contains 0.15/0.25% molybdenum and 0.80/1.10% chromium, making it an optimal choice for many industrial and commercial uses. With superior weldability and machinability, E4130 offers an impressive strength to weight ratio and hardness. This makes it an ideal material for a number of applications, such as commercial and military aircraft construction, ground support systems, automotive and race cars, off-road vehicles, hydraulic tools, and machine tool applications.
Property | 4130 (E4130) |
---|---|
Carbon Content | 0.28/0.33% |
Sulfur Content | 0.025 max. |
Molybdenum Content | 0.15/0.25% |
Manganese Content | 0.40/0.60% |
Silicon Content | 0.15/0.35% |
Benedict-Miller’s stocks a large inventory of 4130 alloy steel, certified to Aerospace Material Specifications. With cut and finished products to customer specifications, this reliable supplier offers plate, sheet, round bar, and flat bar (cut from plate). They provide mill certification upon request, and a 100% quality guarantee.
Transitioning into the next section, the manufacturing process of alloy tubing begins with ASTM A513 Type 5 or ASTM A519 industry standards to produce a wide range of sizes. This allows for flexibility in size-specific needs and supports various applications. Stay tuned to learn more.
ASTM A513 Alloy Steel Tubing
Offering a range of benefits, ASTM A513 provides durable, tight-tolerance alloy steel tubing for various industrial, agricultural, and transportation applications. Manufactured from low carbon steel, the tubing is available in hot rolled black and hot rolled and offers advantages such as durability, tight tolerances, and cost-effectiveness.
ASTM A513 Type 1 and T5 are two of the most common types of steel tubing. Type 1 is manufactured from low carbon steel and allows for bending while T5 provides robust structural support for heavy-duty metal products. ASTM A513 has a variety of uses in a range of industries including agricultural, industrial, and transportation. It offers advantageous qualities and provides structural support for commercial and residential products. The chemical composition of the tubing includes iron, carbon, phosphorus, manganese, silicon, and silver.
ASTM A513 Type 5 Dom Tubing is made using C1020 strip and is formed and electric resistance welded into its basic shape. After annealing, the tubing is cold drawn which produces a uniform grain structure and closer tolerances, uniform wall thickness, and higher physical properties than other types of tubing.
Product Specs:
- Manufactured from low carbon steel
- Formed and electric resistance welded into its basic shape
- Cold drawn after annealing
Pros:
- Durability
- Tight tolerances
- Cost-effectiveness
- Wide range of applications
Cons:
- Not suitable for very high temperatures
ASTM A519 Grade
ASTM A519 grade is a type of alloy steel tubing manufactured to industry standards for a variety of applications. Alloy steel properties such as superior tensile strength, high strength to weight ratio, and machinability make it an ideal candidate for processing techniques where strength is required. It is heat treatable to a broad range of strengths, and can be treated to provide a range of hardnesses. Applications include automotive and transportation, aircraft frames, bicycle frames, shafts, collars, roll cages, control arms, and A-arms.
Sizes of alloy steel tubing are available in a large range of OD and wall thickness dimensions, and can be rolled bar or pierced or cold drawn to meet specific size requirements. This makes it a great option for streamlining the supply chain, since Metal Special has the inventory and capabilities to meet material needs. High-quality alloy steel tubing is available in a variety of grades and types, with 4130 and 4140 being the most common. Minimal stock allowance is needed for clean-up due to its excellent machining characteristics.
MANUFACTURING PROCESS for Alloy Tubing
Alloy steel tubing is manufactured per ASTM A513 Type 5 or ASTM A519 industry standards. The two standards differ in terms of their material grades, types, and specifications. Manufacturing processes include CDS, HRS, and DOM. Each of these processes has its own advantages and applications.
The machinability of alloy tubing also depends on its grade, with 4130 and 4140 being the easiest to machine among common alloy grades.
The range of sizes available makes alloy tubing a great choice for many applications. Its superior tensile strength and toughness, along with its high strength-to-weight ratio, make it an excellent candidate for most processing techniques. It also has excellent machining characteristics and can be heat treated to a broad range of strengths, machinabilities, and hardnesses.
Metal Special has been a leading metals distributor for over 60 years. With their inventory, resources, and capabilities, they are well-equipped to meet material needs. With their on-time delivery within budget and customized cut lengths available, they are the perfect supplier for alloy tubing.
Alloy steel tubing offers a wide range of benefits, making it a great choice for automotive and transportation, aircraft frames, bicycle frames, shafts, collars, roll cages, control arms, and A-arms. Its advantages make it an ideal option for those who need strength and precision.
With the transition into the subsequent section about benefits of alloy round mechanical tubing, let us further explore these advantages.
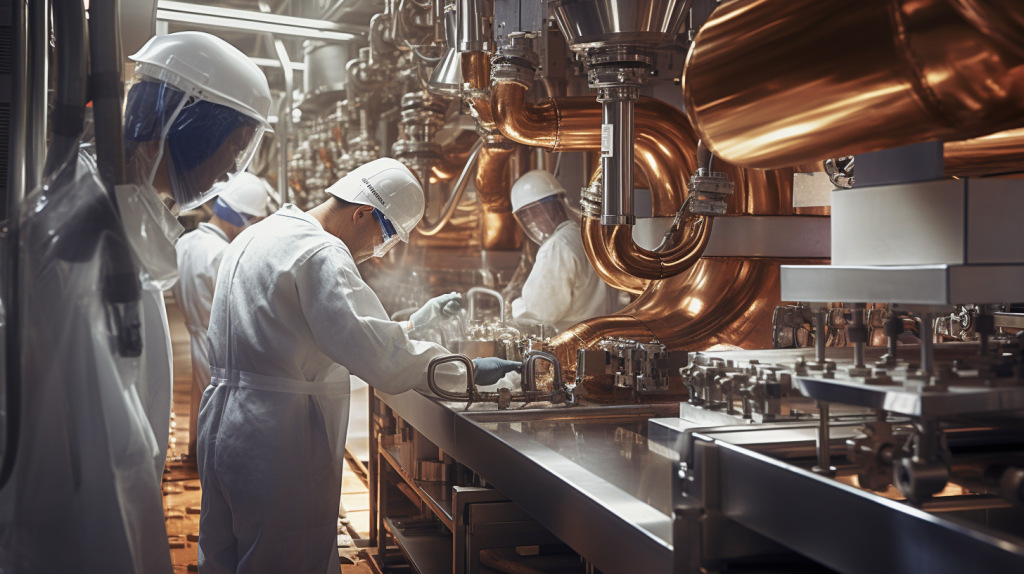
BENEFITS OF ALLOY ROUND MECHANICAL TUBING
With its superior tensile strength and toughness, along with its high strength-to-weight ratio, alloy round mechanical tubing offers numerous benefits. This type of tubing is easily heat treatable to a broad range of strengths, machinabilities, and hardnesses, making it an excellent candidate for most processing techniques where strength is required. Alloy round mechanical tubing is available in a wide range of sizes, providing options to meet size-specific needs and supporting a variety of applications.
The machinability of 4130 and 4140 alloy tubing makes it the easiest to machine among common alloy grades, with minimal stock allowance needed for clean-up. This type of alloy tubing exhibits excellent machining characteristics due to its medium carbon alloy composition. It is a great choice for machined parts, wear parts, fixtures, mold bases, gears, and more.
When considering alloy round mechanical tubing as an option, it is important to understand what product specs, pros, and cons are associated with it.
Product Specs:
- Alloy tubing is produced per ASTM A513 Type 5 or ASTM A519 industry standards.
- Different manufacturing processes include CDS, HRS, and DOM.
- ASTM A513 Type 5 is used for certain grades and types of alloy tubing.
Pros:
- Superior tensile strength and toughness.
- High strength to weight ratio.
- Easily heat treatable to a broad range of strengths, machinabilities, and hardnesses.
- Excellent candidate for most processing techniques where strength is required.
- Many options available due to the range of sizes produced.
Cons:
- Can be more expensive than other materials.
- May require special machining techniques for certain applications.
- May require more frequent maintenance.
APPLICATIONS BY INDUSTRY
The machinability of alloy steel tubing makes it a suitable choice for a wide range of industries, from automotive and transportation, to aircraft frames, bicycle frames, and more. This type of tubing is often used for key components in these industries, such as shafts, collars, roll cages, control arms, and A-arms.
The following are some of the most common applications for alloy steel tubing:
- Automotive Applications: Alloy steel tubing is often used in automotive applications due to its superior strength and toughness. It can be used for drive, half, and prop shafts, as well as other components like collars and roll cages.
- Aerospace Applications: Alloy steel tubing is also used in the aerospace industry for aircraft frames and other components. It is especially suited for this type of application due to its high strength to weight ratio.
- Oil and Gas Industry Uses: Alloy steel tubing is a common choice for the oil and gas industry due to its strength and machinability. It is often used for wear parts, fixtures, mold bases, and gears.
Alloy Steel vs. Carbon Steel
Building on the machinability of alloy steel tubing, it is also important to consider the differences between alloy steel and carbon steel when selecting a type of steel for an application. Alloy steel contains alloying elements such as aluminum, chromium, copper, manganese, nickel, silicon, and titanium, and offers improved strength, hardness, wear resistance, and corrosion resistance compared to carbon steel. Carbon steel contains carbon as the main alloying element and is known for its strength, durability, and heat-treatability.
Alloy Steel | Carbon Steel |
---|---|
Strength and Durability | Strength and Durability |
Heat Treatment | Heat Treatability |
Machinability | – |
Corrosion Resistance | – |
Application Suitability | – |
Alloy steel can be heat-treated to increase strength and hardness, and is resistant to wear and tear. It is also ductile, magnetic, and can be used in electrical applications. Carbon steel is more susceptible to rust than other types of steel. Each type of steel has unique properties and applications, and the choice between alloy steel and carbon steel depends on the application. Alloy steel is used in the construction, automotive, aerospace, energy, and manufacturing industries, while carbon steel is used in construction, automotive, oil and gas, infrastructure, and manufacturing industries.
Types of Alloy Steel
There are two types of alloy steel: low-alloy steel and high-alloy steel. Low-alloy steel contains elements like aluminum, chromium, copper, manganese, nickel, silicon, and titanium. These elements enhance the mechanical properties of the steel and are commonly used in the construction, automotive, and aerospace industries.
High-alloy steel contains more than 5% of elements like chromium, vanadium, or tungsten and is used in applications like machine tools, wear parts, and mold bases.
The alloy steel grades vary depending on their alloying elements, heat treatment methods, and properties. Alloy steel is resistant to wear and tear, can be heat-treated to increase strength and hardness, and is ductile and easily formed into different shapes. It is magnetic and can be used in electrical applications, has a low melting point, and can be welded easily.
Tool steel is a type of alloy steel with high carbon content and other elements like chromium, manganese, and/or tungsten.
Alloy steel is widely used in industries such as construction, automotive, and power generation due to its improved strength, hardness, wear resistance, and corrosion resistance compared to carbon steel. It is also used in the production of high-strength parts like gears, shafts, and axles.
The choice between alloy steel and carbon steel depends on the specific application and requirements.
Frequently Asked Questions
What Is the Difference Between Alloy Steel and Carbon Steel?
Alloy steel is composed of carbon and other elements that provide increased strength and hardness, as well as improved corrosion resistance and machining processes. Heat treatments are used to further enhance these properties, making alloy steel a tougher and more durable material than carbon steel.
What Are the Different Types of Alloy Steel?
Heat treating, corrosion resistance, and strength to weight are just a few of the advantages of alloy steel. With its improved mechanical properties and greater versatility, it is an ideal material for many applications.
What Are the Benefits of Using Alloy Round Mechanical Tubing?
Alloy round mechanical tubing has superior tensile strength and toughness, high strength-to-weight ratio, and excellent heat treatability for various strength, machinability, and hardness properties. It also offers superior corrosion resistance.
Are There Any Special Considerations When Manufacturing Alloy Steel?
When manufacturing alloy steel, heat treatment, surface finish, and hardening processes should be taken into consideration. These processes affect the material’s strength, ductility, and machinability, as well as its final characteristics.
What Are the Applications of Alloy Steel in Different Industries?
Alloy steel is used in many industries, typically for cold forming, heat treatment, and welding techniques. It offers superior strength, toughness, and machinability compared to other steels. Alloy steel is a popular choice for automotive, aerospace, and oil and gas industries due to its strength and durability.
Conclusion
Overall, alloy steel tubing provides superior strength, machinability, and a high strength-to-weight ratio compared to traditional steel.
With its wide variety of grades and sizes, alloy steel tubing is suitable for use in a range of industries, from commercial aircraft and automotive to oil and gas.
One interesting statistic to note is that alloy steel tubing is up to 25% lighter than carbon steel, making it an ideal material for applications requiring lightweight, durable components.